PET Bottle Recycling Line for Bottle-to-Bottle Application in Indonesia
Time
11/2020
Area
Indonesia
Capacity
4.5 tons/hr
Application
Bottle to Bottle
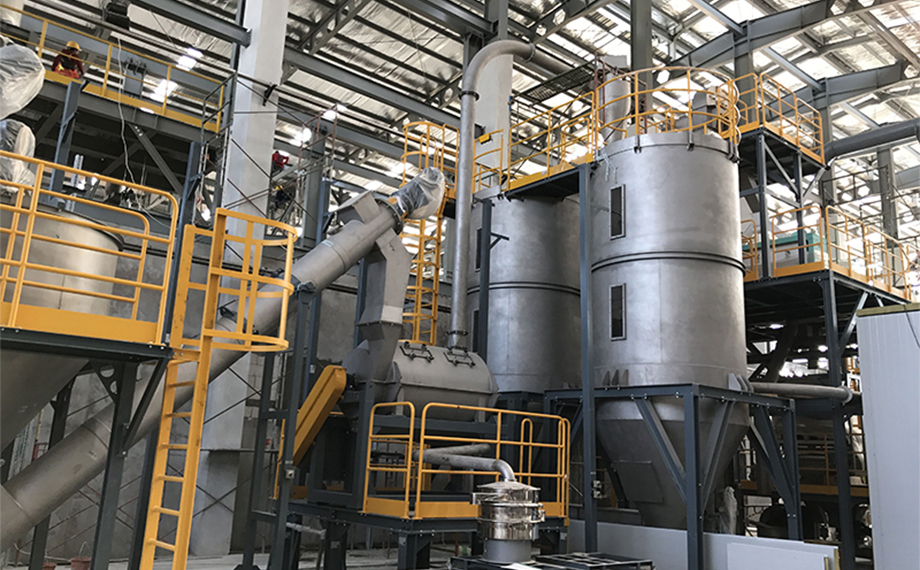
This is a PET bottle-to-bottle project in Indonesia invested by a French
leading environmental group which is a benchmarking enterprise in the field of
global resource optimization management. This group focuses on waste recycling,
water treatment, and energy industries, its business scope covers five
continents. BoReTech was responsible for PET bottle recycling equipment and
engineering service supply, including the whole plant design, installation, and
commissioning guidance in this PET bottle-to-bottle project. The input capacity of this food-grade PET bottle recycling line is
designed with 4.5 tons/h and the output designed capacity is 3.2 tons/h. The
extrusion section and SSP of this project are supplied by EREMA and Buhler. The
final product is food-grade PET chips, which are supplied to a big French group for
PET bottle blowing.
The project was launched in October 2018 and delivered to customers for
production in February 2020. The layout of the PET bottle
recycling line occupied about 2,500㎡.
As the available plant area is limited, BoReTech finally decided to
adopt a compact layout design after several technology meetings with the
customer. The compact process layout can achieve the purpose of complete
washing and auxiliary functions, and the reasonable layout is
convenient for daily maintenance.
The washing process design is mainly aimed at the bottle bale in Indonesia, whose labels are usually removed manually firstly. However, considering the various quality of PET bottle bales, the label separation function is designed as an optional device standby to cope with bottles with PVC labels. The PET bottle bales input capacity is controled through adjusting the speed of the weighting belt conveyor , and real-time monitoring and automatic adjustment of the feeding speed of chain conveyor is conducted to realize operation automation.
Meanwhile, the output capacity is
monitored in real-time to ensure the production efficiency of rPET flakes.
Equipped with multiple metal separation devices, the metal impurities are
automatically removed and collected inline. PET bottle washing line is also
equipped with an automatic bottle sorting machine, automatic flake sorting
machine and flakes oversize sieving device. Through the
detection of PET flakes, the oversize flakes will be crushed for a second time.
The small size flakes are collected through the dust removal system to ensure
the productivity of rPET flakes and reach food-grade PET flakes quality requirements.
The dust removal system realizes high automation of PET bottle recycling and
provides a clean and hygienic environment for employees in the workshop.
The automatic detergent dosing system and the inline water-saving system
can filter and recycle the chemical water. After online 3 steps filtration, the
PET flakes and chemicals are completely separated to realize water recycling
and reuse inline. At the same time, it helps customers save 1kg chemical cost
of PET flakes per ton output and reduce 100kg/h steam consumption.
The electronic control design adopts the SCADA system which was independently
developed by BoReTech. PLC combined with a computer can achieve remote control.
The real-time production situation of the washing line can be checked and
monitored in front of a computer, and the PET bottle washing line operation can
be controlled directly by remote. Meanwhile, it has
functions such as equipment maintenance guidance and production report
generation.
In addition, the safe and standard design of wire and cable, pipeline,
and platform are fully in accordance with European standards, international
standards and the configuration of equipment’s spare parts for models, which is
convenient for equipment’s daily maintenance and repair.