Generates Millions in Added Value Annually
FRS300
Antecedentes
01
Raw Material Loss Costs
In virgin polyester fiber spinning production, waste is generated due to unstable process parameters, improper operator actions, equipment failures, or product line switches. For example, a company producing 100,000 tons annually with an industry-average waste rate of 1% can reduce raw material loss by 1,000 tons using Boretech’s FRS300 system, adding millions in value annually.
02
Regulatory Restrictions on Waste Handling
Under the General Industrial Solid Waste Management Regulations, waste must be registered as "industrial solid waste," increasing logistics costs by 15%-20% due to transfer documentation requirements. Improper disposal may result in fines of 50,000–100,000 RMB per incident. The 2025 updated Green Factory Evaluation Standards for the Chemical Fiber Industry mandates a comprehensive waste utilization rate of ≥95%.
03
Limitations of Traditional Recycling Technologies
Physical recycling methods require high-temperature melting, leading to oxidative degradation and low-quality output unsuitable for same-grade recycling. Additionally, these methods consume significant electricity and produce large amounts of waste gas and water, resulting in high recycling costs.
Feature
- Eliminates waste accumulation with real-time, on-site recycling.
- Reduces costs through self-sustaining cycles. For a 100,000-ton annual production line with 1% waste, adds millions in value.
- The process is wastewater-free, emission-free, and low-energy, avoiding degradation and yellowing issues associated with traditional waste-to-flake methods.
- Supports corporate ESG goals and zero-emission green manufacturing.
Description
The FRS300 is an integrated, fully automated system that processes polyester waste through shredding, pelletizing, and fine grinding to produce PET powder with a particle size of 0.3-1 mm. The entire process employs low-temperature technology, preserving the material’s properties and enabling same-grade recycling without wastewater or gas emissions.
The recycled PET powder is blended with PTA and undergoes esterification, pre-polycondensation, and final polycondensation to produce PET melt of the same quality as virgin PTA-based polymerization, achieving a fully closed-loop recycling system for polyester waste.
This system is tailor-made for virgin synthetic fiber production enterprises. Through innovative processes, it instantly converts production waste into high-quality PET+ powder, which is directly reintroduced into CP polymerization units. This achieves zero loss in fiber spinning, resolves the challenges of resource waste and downgraded recycling, enhances the competitiveness of synthetic fiber products, and delivers groundbreaking economic and environmental benefits.
Truly realizing a zero-loss cycle of "waste → raw material → new product"!
Core Process Flow
Feeding → Shredding → Metal Removal → Pelletizing → Fine Grinding → Dust Removal → Packing
Input Capacity
300 kg/h
Dibujo 3D
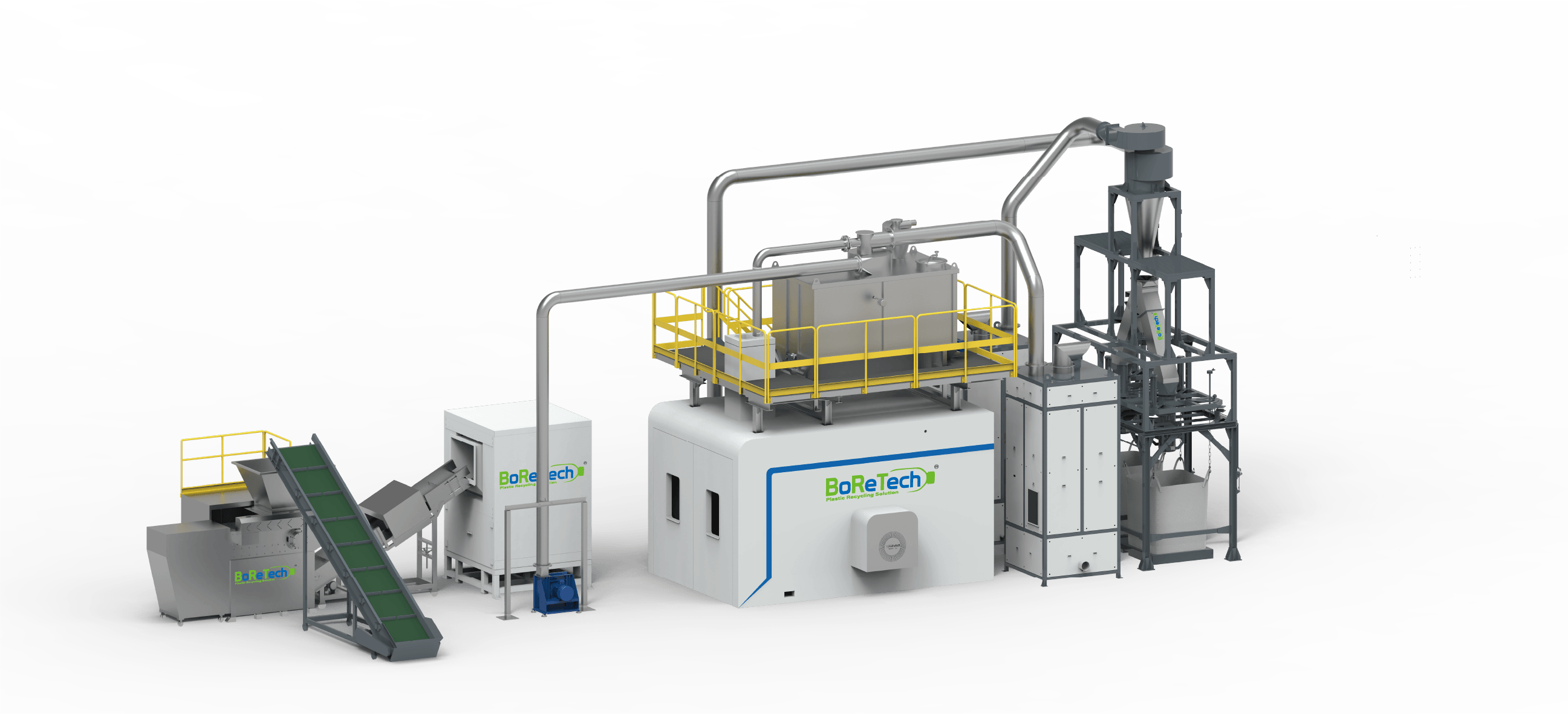